In Search of a Better Way: Adjusting Shrimp Trawl Gear
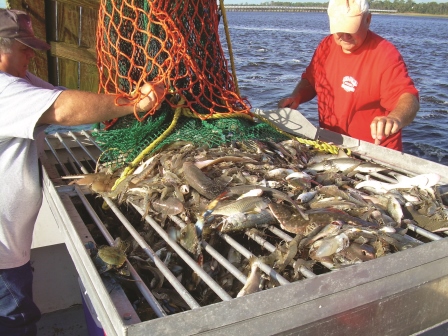
During the holidays, visions of shrimp may dance in many heads, from shrimp cocktail to shrimp towers to shrimp kebabs. But while it might be easy to pluck these crustaceans from festive platters, harvesting them from state waters is more involved.
In North Carolina, bottom trawlers catch shrimp by pulling nets in tows that typically last 30 minutes or longer. Once they bring the catch on board, shrimpers have to sort through their haul, which is time and labor intensive. Besides shrimp, their load often includes unintended catch, or bycatch, such as sharks, rays and jellyfish that have to be returned to the water.
Hauls with a lot of bycatch reduce trawler fuel efficiency and increase the time needed to manually cull the catch. In some instances, high bycatch-to-shrimp ratios may result in bruised or crushed shrimp, producing an inferior-quality product.
John Broome, a Wilmington-based shrimper, conducted two projects that tested shrimp gear changes. His research ideas were supported by the N.C. Fishery Resource Grant Program. The FRG program, as it also is known, is administered by North Carolina Sea Grant.
“We proposed to come up with new gear that would help us cull the catch out faster and also get the bycatch back into the water faster,” Broome explains. Quick processing preserves the quality of the shrimp and helps the bycatch survive.
“When you have bycatch, I think it’s important to get it back into the water and try to keep everything alive,” he continues. “It’s good for the industry and it’s good for the environment.”
Scott Baker, Sea Grant fisheries specialist, sees a win-win situation. “This is a case where shrimpers and fishery managers want the same thing: Make the shrimp fishery both more efficient and more selective in the harvest of shrimp,” he says.
A GRATE-FULL OF CATCH
Broome’s initial FRG project added two grates and a flooding method to his culling process in an attempt to reduce the sorting time for shrimp and bycatch. This three-part culling process could be used individually or in combination. He bottom-trawled in the ocean between Carolina Beach and Oak Island, and in the Cape Fear River.
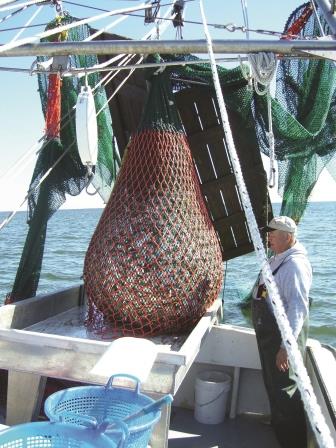
“The whole purpose is to minimize the unwanted aspect of shrimping, which is dealing with bycatch,” Baker explains.
Another intention was to preserve the quality of the shrimp through quicker culls. “The sooner you can get the bycatch separated, the sooner you can get the shrimp into their final place — whether that’s ice or brine or anything to get it processed,” he adds.
First, Broome built a culling efficiency sorter, or CES, which was a grate with bars spaced 2 inches apart, for the top of his culling box. When he emptied the tailbag — which is the end of the net where the shrimp are caught — on the table, the CES trapped the bigger bycatch while the smaller shrimp fell through.
“Before it even got to the bottom of the box, we were able to capture a lot of the bycatch,” he recalls. Broome and his mate removed marketable fish before scraping other fish and debris into the water with culling rakes. The top CES allowed Broome to return unwanted species quickly to the water, ensuring lower mortality for bycatch.
It was a work in progress, as he adjusted his methods throughout his trawls to find a workflow that would make culling safer and more efficient. Initially, he used a shaker motor to move the shrimp off the grate. However, when he found that the vibrations caused more bycatch to drop into the culling table, he stopped using it.
Second, Broome flooded the box in hopes that the fish would float and the shrimp would remain at the bottom of the table. Although this method didn’t work as well as expected, the water had several advantages.
Quickly flooding the shrimp helped preserve their quality by cooling them and reducing bacterial activity, particularly if the shrimp had died. Further, the water lifted the heavier fish off the smaller crustaceans, reducing the chances of the shrimp being bruised and easing the process of separating the shrimp from bycatch.
Finally, Broome had another grate at the bottom of the table with 1-inch separations between the bars that he would raise to remove more bycatch. At the end of this process, “we were left with almost pure shrimp sometimes,” he notes, which was good for the shrimp — and for his business.
“When you’re culling, you’re having to go through everything and you’re using culling rakes and you’re pulling things through. I think that it just seemed to me that the shrimp were not bruised or damaged as much because you didn’t have that much material to sort through. It seemed to me like a better-quality product,” Broome says.
Baker agrees. The CES is “good at removing large items quickly and may remove some other items as well. And, although not tested, by having a wet culling table, it basically allows the shrimp to be of higher quality,” he adds, noting that potential future projects could measure the quality of the shrimp.
OUTSIDE THE BOX
The success of the CES got Broome thinking outside of the (culling) box to the turtle excluder device, or TED, in his nets. “If we could eliminate a lot of the bycatch by using that top grate, why not incorporate it into the TED itself?” he asked. Federal law requires him to use TEDs in his trawl nets to prevent turtles from getting trapped in the end bag.
For his second project, Broome experimented with 2-inch spacing for his TEDs. The shrimper wanted to compare the relative effectiveness of the standard and reduced spacing. “As far as I know, I was the first to use and conduct research by comparing a 4-inch grid TED to a 2-inch grid TED on the East Coast,” he says.
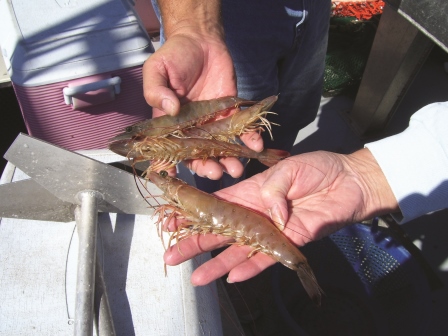
Regulations state that 4 inches is the maximum distance between the TED bars for shrimp trawls, but do not specify a minimum spacing.
“Those bars are spaced at 4 inches because that’s the width of a carapace, from belly to the top of a turtle,” explains Sara Mirabilio, Sea Grant fisheries specialist. “Anything bigger than that would trap turtles.” See story on page 16 for Mirabilio’s project to test a new TED design for the flounder trawl fishery.
In trawl nets, the TEDs are angled to guide any turtles or other larger creatures that enter the net to an opening that allows them to escape. Smaller fish and shrimp slip through the bars of the TED into the bag end of the net.
Broome figured that a TED with smaller spacing might keep more bycatch out of his end bag. But he was concerned that the change also might affect his catch.
“After I put up for the project and it got approved, I thought I was setting myself up for a lot of shrimp loss,” Broome admits. But he plunged gamely into the research.
“The bycatch was decreased by using the smaller spacing but the shrimp catch was the same, which is great,” Sea Grant’s Baker notes. Less bycatch means the shrimpers could lower their fuel costs by pulling lighter loads. In addition, smaller hauls improve safety for the crew because they do not have heavy nets swinging at the back of their boats.
On average, the standard TED caught about 30 pounds of shrimp per tow compared to the reduced-grid TED that bagged 28 pounds, for a difference of two pounds. “And on over half of the tows,” Broome continues, “the net that had the 2-inch grid actually caught more shrimp.” He conducted his tows between Carolina Beach and Lockwood Folly inlets.
Steve Parrish, owner of S&S Trawls in Supply, makes TEDs for shrimp trawlers in this country and around the world. He assembled the narrow-grid TED for Broome, but he also builds them for many of his customers in and outside the state, with spacing varying between 2 and 4 inches.
It was Parrish who advised Broome on the minimum spacing for his bars. “Anything less than 2 inches will cause a great amount of shrimp loss, especially for larger shrimp,” the TED builder warns.
For his shrimp-trawling customers, reduced-grid TEDs are fairly popular. “Just about all fishermen use them at some time or another,” Parrish says. They are a tool that shrimpers can use at different times of the year to reduce bycatch while maintaining their haul.
Parrish calls these narrow-grid TEDs jellyball TEDs. Broome quickly discovered why. Jellyballs are a nickname for cannonball jellyfish that are similar in size and appearance to their namesake missile.
“By using the 2-inch reduced-grid TED, it knocked most of the jellyballs out,” Broome confirms. In addition, he could keep shrimping without having to stop to unclog his TED of jellyballs.
SEEKING A WILLING AUDIENCE
In Broome’s eyes, both projects were resounding successes — and he is ready to spread the word. “We conducted outreach by creating a pamphlet and distributing them at local net shops and regional commercial fishing establishments,” he says. As a result of his and Sea Grant’s efforts, several shrimpers have contacted Broome for more information about his gear changes.
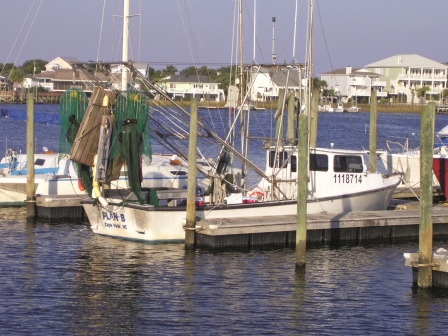
“Anybody that will stand still long enough, I’ll tell them what a benefit this is,” he continues.
These days, Broome still uses the CES gear. “We flood the culling box now and we also use the top grate. And occasionally, if we have the right kind of bycatch — if it’s smaller — we will use the bottom grate too,” he explains.
In addition, he uses the 2-inch reduced-grid TED, together with a combination of the CES gear. This gives the bycatch two chances to be culled quickly. On occasion, his culling times are a quarter of what they would be if he didn’t use either gear.
For Broome, every step to improve the quality of his shrimp is worth it. “That’s why even though that 2-inch reduced grid takes a lot of the bycatch out, I still incorporate this other [CES] method of culling and that helps even more,” he says. Other positive side effects include safer shrimping conditions because of lighter hauls and reduced labor costs because there is less bycatch.
“We’re getting a better-quality product and we’re also getting the bycatch back into the water faster, so there’s less mortality and that’s important too,” Broome adds. “The more we can do in this industry to help the bycatch and to reduce the mortality, the better position we’re in.”
To read Broome’s final Fishery Resource Grant reports, go to: www.ncseagrant.org. Search for 09-FEG-01 for the CES study, and for 10-FEG-03 for his reduced-grid TED project. Visit: www.ncseagrant.org/s/shrimp-gear for a Blueprint summarizing Broome’s recommendations.
SHRIMP FISHERY MANAGEMENT PLAN UPDATE
Through September and October, the N.C. Division of Marine Fisheries, also known as DMF, sought public comments for its five-year revision of the Shrimp Fishery Management Plan, or FMP. Currently, one of the FMP’s recommendations is to continue research in the shrimp trawl fishery and investigate how this method affects habitats.
The N.C. Marine Fisheries Commission, or MFC, can either pursue a revision, which involves updating the data and fishery-related information in the plan, or an amendment process to explore changes in management strategies. In a September announcement, DMF said that there are no plans to make any amendments to the Shrimp FMP.
The MFC will decide how to proceed with the new FMP at its November meeting. Visit: portal.ncdenr.org/web/mf for the latest information on MFC actions.
This article was published in the Holiday 2012 issue of Coastwatch.
For contact information and reprint requests, visit ncseagrant.ncsu.edu/coastwatch/contact/.